North Queensland Cane Farm
Energy Savings: 49.7% | Cost Savings: $56,000 | Capital Cost: $250,000 | CO2 Savings: 9.6 tCO2-e | Project Status: Proposed
Industry:
Sugarcane
Location:
Dry Tropics
Pump Type:
Centrifugal
Irrigation Type:
Centre Pivot, Flood, Travelling gun
Technology:
Irrigation and Pumps
The energy audit at a North Queensland cane farm demonstrated the value in an energy audit to check the performance of irrigation systems.
The pump station is a large electricity user some years, that is, it uses over 100,000 kWh of electricity in dry years where more irrigation is required.
The site has a 30kW Solar PV system. As the site is classified as a large user, it does not receive a solar feed in tariff for any exported electricity.
The graph below shows the seasonality of the site, with electricity consumption, demand and solar export.
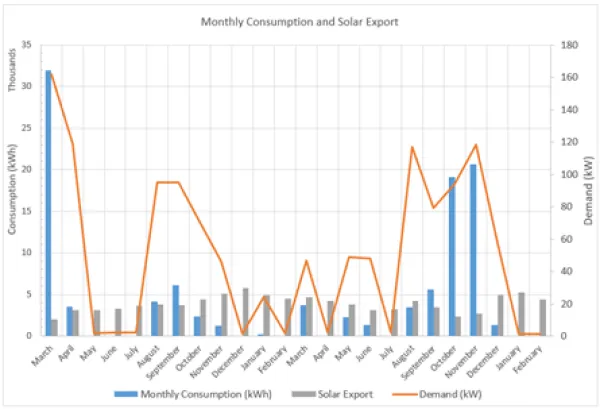
This second graph shows the impact of the Solar PV system on energy consumption over a 24 hour period where the 45kW pump was running consistently.
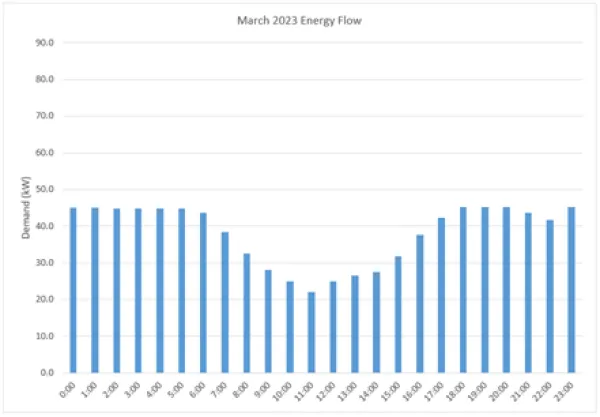
The audit considered one of 3 pumps in a pump station. Each of the pumps have a range of duties with various irrigators connected to each pump including pivots, laterals, travelling guns and flood. The irrigators are different distances from the pump station.
The pump selected for the audit was a Southern Cross pump with a 45kW motor that irrigates 207 hectares of cane and the audit was conducted based on energy consumption over two fairly wet years (Figure 1) so the energy consumption was relatively low.
The auditor took various measurements of water flow and energy consumption and found that the pump and motor were operating well at around 4 kWh/ML/m.
It was noted however, that the suction flow rate was 30.9 litres per second (L/s) and the flow rate at one of the irrigators had decreased to 16.7 L/s indicating a loss of 14.2 L/s of water through the pipe network.
The audit recommended that a Certified Irrigation Designer be engaged to look holistically at the irrigation system.
The audit provided the example recommendation based on upgrading 4,700m of mainline irrigation pipeline from 150mm to 200mm diameter pipe to reduce friction losses, thereby reducing total dynamic head (TDH). This would reduce friction losses by 50m of head and reduce energy usage from 393.6 kWh/ML to 197.9 kWh/ML.
The anticipated savings from the upgrade are shown in the table below.
Recommendation |
Estimated Cost to Implement ($) |
Electricity Savings (kWh/p.a.) |
Emission Reduction (tCO2-e) |
Maximum Demand Saving (kW) |
Estimated Opex ($/p.a.) |
Estimated Electricity Savings ($/p.a.) |
Total Estimated Savings ($/p.a.) |
Payback Period (years) |
Upgrade pipeline network |
250,000 |
10,936.3 |
9.6 |
21.8 |
51,903.16 |
4,224 |
56,031.72 |
4.5 |
The Operational (Opex) savings identified in the table above include:
- Recovery of the lost water (14.2 L/s)
- Potential increase in productivity by applying the ‘lost’ water to crops
- Additional savings in being able to operate 2 laterals at once with increased pipe capacity.
A couple of notes about the upgrade:
- It is likely that an upgrade of the main like will change the duty points of the irrigation system significantly, which may require change of pump. There are three pumps at the pump station: one of which has a VSD installed. A detailed irrigation system design would need to be done to consider the changes.
- The savings estimates in Table 1 are based on years with low irrigation, so the potential savings would be greater in dryer years where more irrigation is required.
The Case Study is featured in the Pumping Energy Efficiency webinar presented by Phil Szabo who was the auditor for the site. Watch the Webinar on the Ag Energy Hub HERE.
Energy Audits. The farm had a Type 3 energy audit as a participant in the QBEST Ag program.
For more information about Choosing Solar Systems, see the Ag Energy Hub Solar Article HERE.
The program was delivered by the Queensland Farmers’ Federation and funded by the Queensland Government.