Queensland Beef Processors
Energy Savings: 17% | Cost Savings: $107,161 | Capital Cost: $455,500 | CO2 Savings: 541 | Project Status: proposed
Industry:
Beef
Location:
Border Rivers
Pump Type:
Centrifugal
Irrigation Type:
Drip
Technology:
Irrigation and Pumps, Solar Power and Renewables
The accumulated annual electricity consumption of the six processors during the 2015-2016 period was 2,736,000 kWh at the cost of $482,900. The annual gas consumption for the group was estimated at 2,330 GJ with a cost of $97,500. The energy consumption on the sites consists mainly of:
- Condensing units servicing cool rooms and freezer rooms.
- Refrigerators, display cases and refrigerated containers.
- LPG water heaters and heat pump water heaters.
- Wood and oil-fired boilers.
- Manufacturing line equipment.
Energy audits showed how improving the current systems can lead to energy and cost savings. The main recommendations from the audits include:
- Power factor correction (PFC) equipment: installing a 100 kVAr PFC unit at the Plainland site to reduce reactive power use. Install another unit at the Esk site as well.
- Evaporator fan speed control: at the Maclagan, Warwick and Chinchilla sites to regulate the speed to the optimal level.
- Lifting the compressor suction pressure: at the Maclagan site to increase the evaporator temperature from -20°C to -10°C, which is optimal. This solution will also involve replacing the current evaporator with a larger unit and insulate the suction line.
- CO2 heat pump: install a 150 kW heat pump at the Biggenden site to generate hot water efficiently at 60°C for washdown requirements and pre-heat sterilisation water to replace the existing LPG burners. A 30kW CO2 heat pump has been recommended for the Esk site and a 4.5kW system for the Chinchilla site for hot water generation.
- Solar PV systems: installing an 80 kW Solar PV at the Warwick site and a 10 kW PV system at the Chinchilla site to offset part of the energy consumption from the grid.
- Refrigeration system and refrigerant replacement.
- Heat recovery solutions.
Table 1. Costs and energy savings from audit recommendations.
Farm | Recommendation | Annual Energy Savings (kWh) | Annual Gas Savings (GJ) | Annual Costs Savings ($) | Capital Cost ($) | Payback Period (Years) |
PLAINLAND | PFC | – | – | 5,062 | 15,000 | 3 |
MACLAGAN | Evaporator fan speed control | 11,700 | – | 2,556 | 15,000 | 5.9 |
Lift compressor suction pressure | 13,250 | – | 2,895 | 13,000 | 4.5 | |
WARWICK | Evaporator fan speed control | 90,000 | – | 19,330 | 76,000 | 3.9 |
Solar PV | 138,500 | – | 21,080 | 122,000 | 5.8 | |
BIGGENDEN | CO2 heat pump | -81,424 | 1,173 (325,833 kWh) | 32,881 | 138,000 | 4.2 |
ESK | PFC | – | – | 4,300 | 6,500 | 1.5 |
CO2 heat pump | -12,046 | 244 (67,778 kWh) | 11,633 | 37,000 | 3.2 | |
CHINCHILLA | Evaporator fan speed control | 6,215 | – | 1,392 | 5,000 | 3.6 |
CO2 heat pump | -2,025 | 36 (10,000 kWh) | 1,432 | 7,000 | 4.9 | |
Solar PV | 20,529 | – | 4,600 | 21,000 | 4.6 |
By implementing recommendations in the audit, the processors could reduce total energy consumption by 17% and costs by 19%, with Carbon emission savings of 541 t/CO2-e per year.
Table 2. Pre and post audit energy and cost savings.
Metric | Pre-audit | Post-audit | Reduction (%) |
Energy Consumption (kWh) including GAS | 3,383,222 | 2,794,912 | 17 |
Cost ($) | 580,400 | 473,239 | 19 |
For more detail about the heat pump recommendations at these meat processors, visit HERE.
For more detail about the evaporator fan recommendations at these meat processors, visit HERE.
An energy audit is a good investment.
An energy audit is a great first step in moving a business towards a more efficient future by reducing energy use, costs and carbon emissions.
The Energy Savers Plus Program was delivered by the Queensland Farmers' Federation with support and funding from the Queensland Department of Energy and Water Supply.
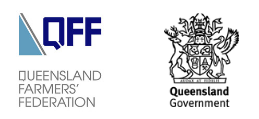